Low Profile Load cell Engineered For Success
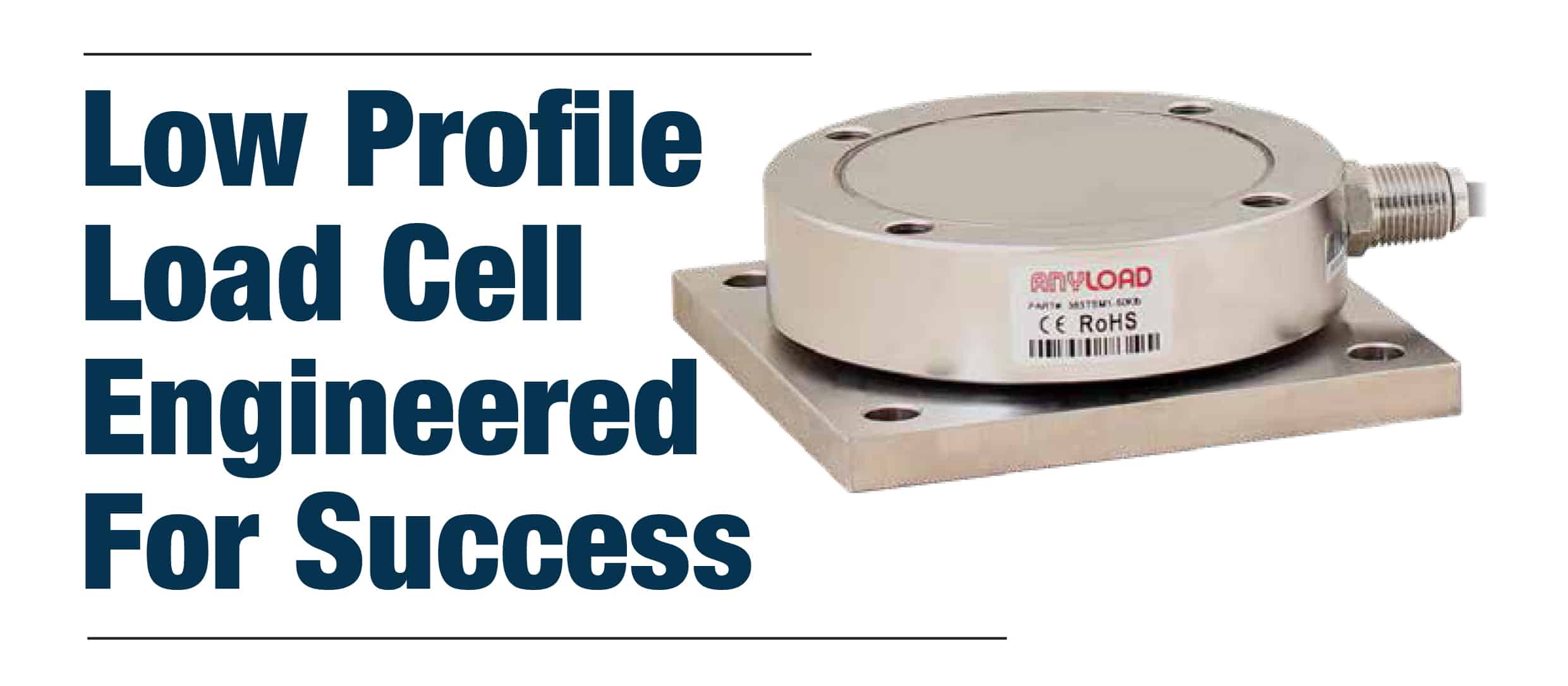
The Project
The Challenges
The challenge consisted of a 50,000-pound capacity compression weigh module with a declared accuracy of 0.05 percent and the desired profile lower than 2.2 inches. This size would be about a quarter of what was common in a weigh module height of 8 inches. In the hopper and tank weighing sector of the process weighing industry, 0.1 percent is considered the high accuracy gold standard. Our Anyload engineers set out to improve the accuracy while remaining within the desired height constraint, or in this case, target. Shrinking a conventional weigh module envelope design was not going to cut it. The Anyload team first sampled a few existing competitive contenders and identified key vulnerable areas needing improvement. One competing product fulfilling the low-profile requirement had only achieved an accuracy of 0.3 percent; hence, short of the target. Another key issue was repeatability (because of movement) of the load cell due to temperature or loading conditions during the actual weighing.
The Results
Amid challenges and in line with our design philosophy focused on reliable products, we crafted our initial prototype, reimagining the load cell’s structure. Moving from a spherical washer to an internalized force loading area with a spherical load pin, we reinforced the cell’s base, enhancing reliability for washdown applications while preserving uplift protection at 50 percent capacity. Our design achieved better accuracy despite weight shifts or tilts up to three degrees, yet higher accuracy remained a challenge due to off-center load movements affecting repeatability.
Addressing this, we revamped the load pin, introducing a convex dimple for a more focused load introduction area, resulting in significantly improved accuracy—0.05 percent versus the standard 0.1 percent. With capacities from 1,000 to 200,000 pounds in stock across our warehouses, our latest models optimize precision and height, even offering a top plate option for easier installation. Collaborative innovation drives us, and we’re committed to pioneering advancements in the industry. Patent pending in Europe and the USA, our engineering team remains dedicated to pushing boundaries.
Help Optimizing Water Efficiency In Stressed Climates
The Project
The Goal
A leading agricultural technology university team is researching ways to optimize plant performance by measuring water consumption efficiently. Their findings are crucial for regions facing water stress. Renowned experts in plant stress physiology and soil and water science aim to ensure future food production despite climate challenges. Their goal is to develop resilient crop strains and processes to improve yields.
In a greenhouse with potted plants, the team uses cooled, humidified air to monitor individual plants’ water consumption continuously. Precise measurement is crucial, and they seek a sensitive system unaffected by temperature variations. This system aims to reduce costs, optimize nutrient delivery, and enhance plant productivity and stress detection, ultimately expediting plant screening.
The Challenges
The Solution
Weighing a Production Platform
The Challenge
The Project
The Method
The Result
China's First Retractable Stadium Roof
The Project
In 2005, we were contracted by Enerpac to manufacture and supply 96 load pins for Nantong Stadium, China’s first retractable stadium roof located in the Nantong, Jiangsu, China. Completed in 2010, Nantong Stadium is a multi-purpose stadium that holds 32,244 spectators and is known for being the world’s first stadium in which the propulsion and stabilisation of the moveable parts take place hydraulically
Load Cell Features
• Materials: Stainless steel and alloy steel
• Capacities supplied: 10t and 150t
• Safe Overload: 150%
• Breaking Overload: 400%
What We Provided
• 88 Stainless Steel 10t Load Pins
• 12 Alloy Steel 150t Load Pins
Split Type Donut Load Cell
Application
Designed to measure and monitor the tension force of an anchor that reinforces the stability of slopes for the prevention of landslides
Installation
Each load cell half was designed with an individual strain gage and individual cable. When installed, the cable from each of the load cell halves are connected with a junction box.
Accuracy Results
• Capacity: 50t
• Safe Overload: 150%
• Breaking Overload: 300%